Understanding High Pressure Die Casting Mold
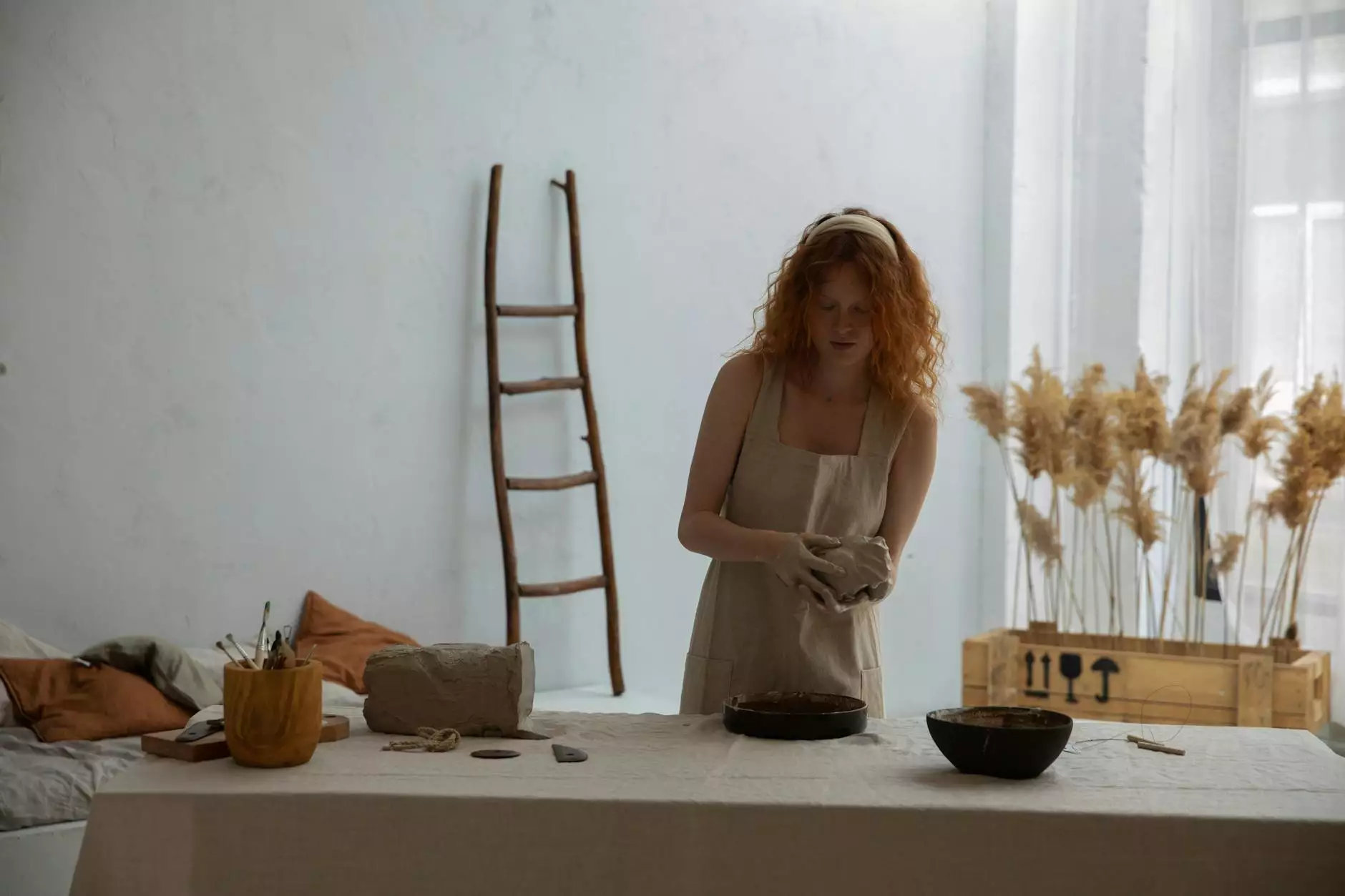
High pressure die casting mold is a vital process in the industry of metal fabrication, offering unmatched precision and efficiency. This article explores the intricacies, advantages, and applications of high pressure die casting molds, illuminating why they have become indispensable for manufacturers around the globe.
What is High Pressure Die Casting?
High pressure die casting is a manufacturing process that involves injecting molten metal into a mold at high pressure. It is predominantly used with non-ferrous metals, such as aluminum, zinc, and magnesium. This method is favored for its ability to create parts with excellent surface finishes and intricate shapes.
The Process of High Pressure Die Casting
The process of high pressure die casting consists of several steps:
- Melt the Metal: The selected metal is melted in a furnace, reaching temperatures that allow for easy flow.
- Injection: Once the metal is molten, it is injected under high pressure into the die (mold), which is preheated for optimal results.
- Cooling: The metal cools and solidifies within the mold, taking the form of the intricate design.
- Ejection: After cooling, the mold is opened, and the finished part is ejected.
The Advantages of High Pressure Die Casting Molds
There are numerous advantages to using high pressure die casting molds in manufacturing, which makes them a preferred choice in various industries:
- Precision and Accuracy: The high pressure involved ensures that even the finest details of a design are captured accurately, producing precise components.
- Surface Finish: Parts produced through this method have excellent surface finishes, often requiring minimal post-processing.
- Enhanced Strength: The process results in parts that have a high tensile strength, which is critical in many applications.
- Cost-Effective Production: High volume production can significantly reduce the cost per unit, making it economically favorable.
- Complex Geometries: The ability to create complex shapes that would be difficult or impossible to achieve with other methods is a game changer.
Applications of High Pressure Die Casting
The versatility of high pressure die casting molds has led to their widespread adoption across multiple industries:
1. Automotive Industry
In the automotive sector, high pressure die casting is used to produce components such as engine blocks, transmission housings, and various structural parts. The strength-to-weight ratio achieved through this process is crucial for enhancing fuel efficiency.
2. Aerospace Industry
The aerospace industry relies on high precision and lightweight materials, making high pressure die casting ideal for producing components like brackets and housings for engines.
3. Electronics Sector
Many electronic devices utilize casings made from die-cast metals for durability and enhanced aesthetics, showcasing the technology's versatility.
4. Industrial Machinery
Industrial machines often require substantial metal components; high pressure die casting provides the needed strength and resilience in harsh operating conditions.
The Future of High Pressure Die Casting
As we advance into a more technology-driven world, the future of high pressure die casting mold looks promising. The introduction of smart manufacturing technologies, such as IoT and machine learning, is set to enhance the efficiency and efficacy of the die casting process.
Innovations and Trends
Current trends and innovations that are shaping the landscape of high pressure die casting include:
- Automation: Automating the die casting process reduces labor costs and increases production rates.
- Sustainability: New technologies aim to minimize waste and energy consumption, aligning with global sustainability goals.
- Advanced Materials: Research into new alloys and composites is enhancing the properties of die-cast components for specialized applications.
- 3D Printing Integration: The combination of 3D printing with traditional die casting opens new possibilities for designing complex molds with optimized cooling channels, leading to better thermal efficiency.
Choosing the Right Partner: DeepMould.net
When it comes to high pressure die casting molds, choosing the right manufacturer is crucial. At DeepMould.net, we specialize in providing high-quality, efficient die casting solutions tailored to your specific needs. Our advanced manufacturing processes and expert team ensure that you receive the best products in the industry, driving your business success forward.
Why Choose DeepMould.net?
Our commitment to quality, innovation, and customer satisfaction sets us apart in the competitive landscape of metal fabrication. Here's what you can expect when working with us:
- Expertise: Our team consists of seasoned professionals with extensive knowledge in die casting and metal fabrication.
- Advanced Technology: We utilize the latest technology and equipment to ensure precision and efficiency in our processes.
- Customization: We offer customized solutions to meet the unique requirements of your projects.
- Quality Assurance: Our rigorous quality control processes guarantee that every product meets the highest standards.
Conclusion
In summary, the process of high pressure die casting molds is a cornerstone of modern metal fabrication, offering numerous advantages that cater to diverse industrial needs. As technology progresses, the future of this technique appears bright, with new innovations enhancing its application and efficiency.
For any business looking to integrate high-quality metal parts into their production lines, deepMould.net is the trusted partner that can help fulfill those needs with excellence. Embrace the future of manufacturing with high pressure die casting and enjoy the remarkable benefits it holds for efficiency, precision, and quality.