Understanding Tube Fitting Dimensions: A Comprehensive Guide
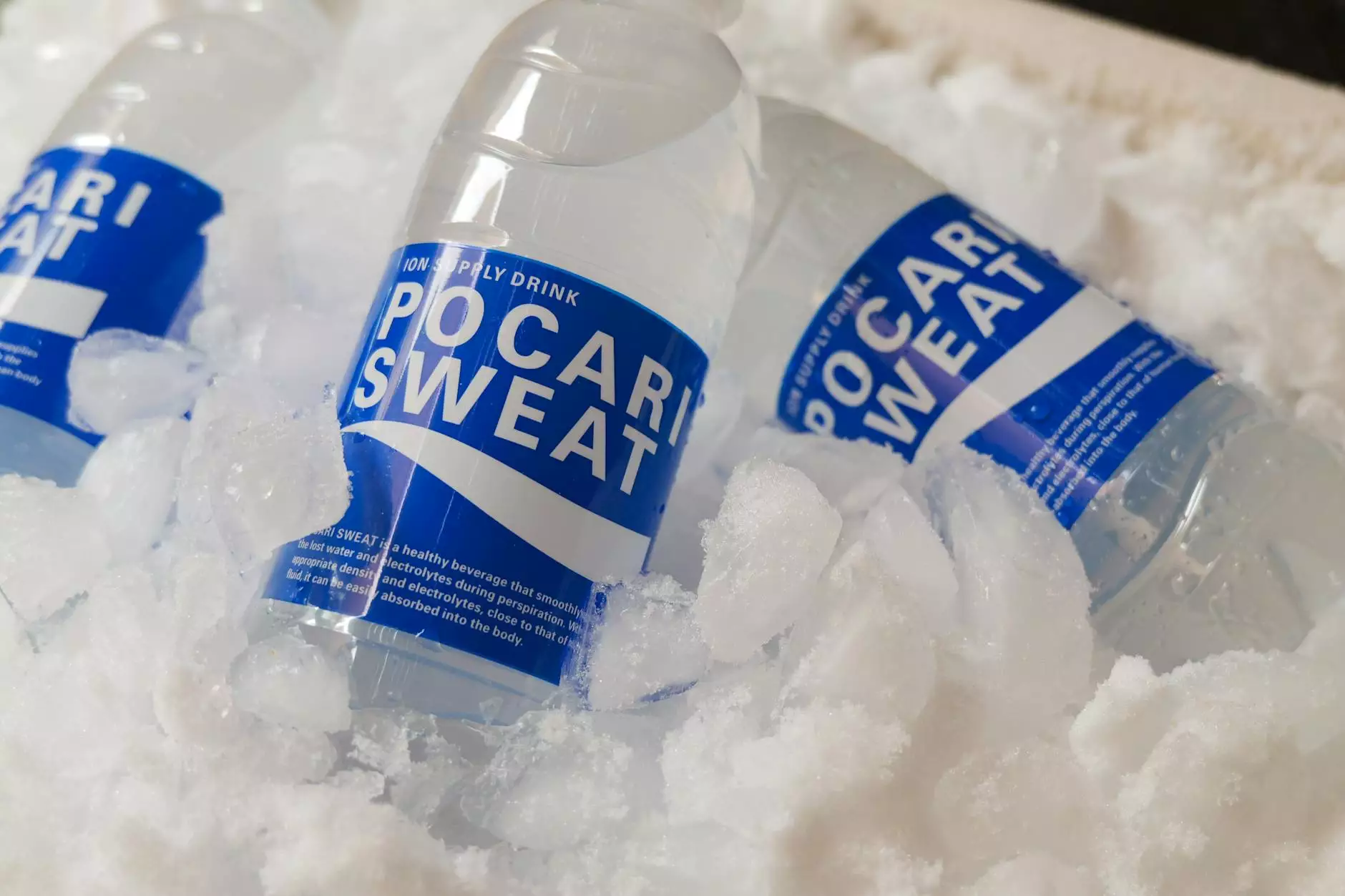
In the realm of engineering and fluid mechanics, tube fittings play a crucial role in ensuring fluid flow and system efficiency. Proper understanding of tube fitting dimensions is not just essential; it is vital for any successful installation or repair.
What Are Tube Fittings?
Tube fittings are connectors that join two or more tubes or pipes together. They can be used in various systems, from plumbing to industrial machinery. These fittings ensure that there is a secure connection capable of withstanding pressure and fluid flow.
The Importance of Tube Fitting Dimensions
The dimensions of tube fittings affect their performance, compatibility with other components, and overall system efficiency. Understanding these dimensions can help prevent leaks, ensure safe operation, and improve the longevity of systems.
Common Types of Tube Fittings
In the market, you will encounter various types of tube fittings, each designed for specific applications:
- Ferrule Fittings: Used primarily in high-pressure applications, these fittings tighten around the tube when pressure is applied.
- Forged Pipe Fittings: Made from a single piece of metal, these provide strength and durability.
- Threaded Pipe Fittings: Easily installed and removed, these fittings are common in plumbing applications.
- Flanges: Used to connect pipes, these fittings provide a flat surface for a secure connection.
- Check Valves: Allow fluid to flow in one direction, preventing backflow.
- Ball Valves: Provide on/off control of fluid flow with a rotating ball mechanism.
- Needle Valves: Offer precise flow control for low flow applications.
- Manifold Valves: Typically used to control multiple lines from a single source.
- Double Ferrule Tube Fittings: Provide a robust seal for high-pressure applications.
- Single Ferrule Tube Fittings: Simplified design for lower-pressure environments.
- NPT Fittings: National Pipe Thread fittings commonly used in various plumbing applications.
Understanding Tube Fitting Dimensions
When selecting tube fittings, it is essential to understand the various dimensions that define their size and compatibility:
Outer Diameter (OD)
The outer diameter of a tube fitting is critical as it determines how well the fitting will fit around the tube. Accurate measurement is vital to ensure a leak-free connection.
Inner Diameter (ID)
The inner diameter is just as important, especially in applications where fluid flow rate is a consideration. The ID can impact the velocity and volume of the fluid passing through the system.
Thread Size and Type
For threaded fittings, thread size and type are pivotal. Different standards, such as NPT (National Pipe Thread) or BSP (British Standard Pipe), offer specific thread dimensions and shapes to ensure compatibility.
Length of Fitting
The overall length of the fitting can affect installation space and, consequently, the system's design. Knowing the required length helps in planning and executing the installation.
Material Thickness
This dimension is particularly important in pressure applications where the walls of the fitting need to withstand considerable stress.
Detailed Consideration for Each Type of Fitting
Now, let's delve deeper into the specific dimensions required for each category of tube fittings offered by TechTubes.in.
Ferrule Fittings
Ferrule fittings typically require precise outer diameter measurements, as they must fit snugly around the tube. Most standards dictate that the ferrule should compress evenly, creating a reliable leak-proof seal.
Forged Pipe Fittings
For these fittings, dimensions traditionally relate to the pressure rating, which is determined by both the material thickness and the inner diameter.
Threaded Pipe Fittings
Thread dimensions are critical. Knowing the correct thread type and size ensures the connections are secure, especially in high-pressure applications.
Flanges
Flange dimensions include bolt hole size, center bore diameter, and the flange thickness; all of which influence the fitting's performance in sustaining pressure and vibration.
Valves (Check, Ball, Needle)
Dimensions for valves often rotate around the diameter of the valve body and the port size. This is essential for maintaining appropriate flow rates within the systems.
How to Measure Tube Fitting Dimensions Accurately
Measuring dimensions can be done with precision instruments. Here are steps to ensure accurate measurements:
- Use Calipers: Digital calipers provide measuring accuracy down to 0.01 mm.
- Micrometers: They are ideal for measuring small dimensions like wall thickness.
- Take Multiple Measurements: Always measure multiple spots to account for any irregularities.
- Record Each Measurement: Keep a log to ensure consistency and reliability in your measurements.
Conclusion
Understanding tube fitting dimensions is fundamental for professionals and enthusiasts in fluid dynamics and related fields. The right dimensions ensure compatibility and optimal functionality, leading to safer and more efficient systems.
Final Thoughts and Best Practices
Whether you’re working on an industrial project or handling a DIY plumbing task, being mindful of tube fitting dimensions will undoubtedly enhance your project outcomes. Choose your fittings from reputable suppliers like TechTubes.in to ensure quality and reliability.
Incorporating precise and reliable measurements into your fittings analysis can set apart successful installations from potential failures. So, invest time in understanding and applying these best practices!